Perforation is the art of forming holes on metal surface. Usually, perforated metals sheets have holes in a predetermined pattern.
Whether you want to know available patterns, sheet metal perforation process, advantages or applications – all information is right here.
Chapter 1: Advantages of Perforated Metals

When you closely examine different objects and equipment around you, you will notice use of perforated metals. From you baking trays, ovens and car radiator hoods, use of perforated metals stems from the benefits they accrue.
Here is why you should consider perforating metals.
Visually Appealing
Aesthetic quality describes aspects that make use of perforated metals visually appealing, such as in the design of a building. Top of Form
For such metal sheets, the perforation pattern typically consists intricate details capable of manipulating entry of natural light.
In fact, there are many decorative perforated sheet metals.
Durability
You can convert any metal sheet into perforated metal, making them highly reliable given the material choice. In applications with humid conditions or corrosive elements, durable perforated metals capable of withstanding damage form such are preferable.
Energy Efficient
Perforated metals can be used to regulate temperature by controlling entry of UV radiation into buildings. Installation of perforated metal in HVAC systems is a sure way to increase efficiency and reduce energy costs.
Pressure Regulation
When used as structural installations on building facades, perforated metals can be configured to regulate pressure by providing wind paths. This is especially true for skyscrapers where pressure spots caused by wind loading are a cause of concern.
Highly Versatile
You can perform forming operations such as bending on perforated metals to suit application needs without difficulty. Perforated sheet metals are common in many applications.
Recyclable
In addition to being energy efficient, perforated metals can easily be recycled, reused and repurposed making them environmental friendly. Consequently, many perforated metals are in line with green global standards and highly applauded in eco-construction.
Sound Proofing
Some applications may require very low noise levels such as those caused by the reflection of sound waves. In such cases, perforated metals can be used to counter such inefficiencies finding use as sound proofing in areas like studios.
Chapter 2: Types of Metals for Perforation Process
Perforation is a vital technique for processing a range of metal materials. However, you may experience varying levels of difficultly. In fact at times, you may require specialized tools and equipment.
Let’s look at some common metals:
Perforating Aluminum
Perforating aluminum is straightforward given its lightweight feature. It is also highly durable with simple installation and its visual appeal allows use in decorative settings such as architecture.

Perforating Copper
Copper’s is a low strength and malleable material than can be transformed into perforated metal for use in applications like interior design. Copper is highly resistant to corrosion forming a protective oxide layer and highly durable while capable of being recycled.

Perforating Titanium
A resolute metal with high strength and corrosion resistant quality, titanium is used in making perforated metal for structural applications. Applications that warrant durable but light material benefit from its low strength to weight ratio.

Perforating Galvanized Steel
Use of galvanized steel is common in making perforated metal sheets for outdoor applications given its resistance to the elements. It is also strong and highly durable to withstand the hardships of outdoor usage.
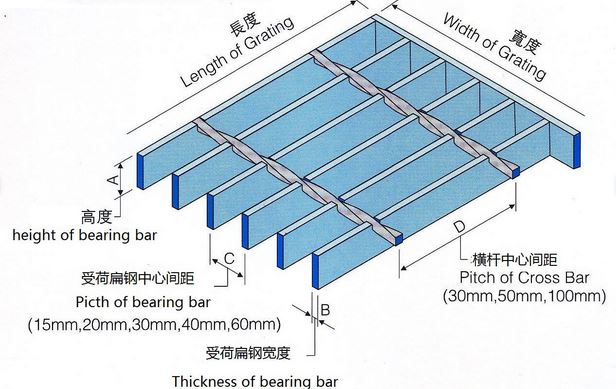
Perforating Stainless Steel
Stainless steel is known for exception corrosion resistance. The chromium component reacts with atmospheric oxygen to form a passive layer of chromium oxide that protects the underlying metal.

Perforating Iron
Iron offers your perforated metal sheet incredible physical properties such as strength and hardness for use in high stress applications. However, its susceptibility to corrosion warrants use in less corrosive environments and surface protection.

Perforating Brass
Combining copper and zinc results in the formation of brass alloy which has improved properties of hardness and deterioration tolerance. Perforating brass is not complicated by virtue of its light nature finding use in aesthetic applications thanks to its visual appeal.

Perforating Nickel
Nickel and its alloys offer good mechanical qualities such as hardness and strength with excellent thermal qualities. The mentioned properties alongside corrosion resistance allow its use in making perforated metals for wet environments.

Chapter 3: Patterns in Perforated Metals
Patterns refer to the arrangement and shape of the holes or openings on the surface of the metal. These patterns can be customized to meet specific design and functional requirements, and vary in terms of hole size, shape, and spacing.
i. Cross Holes: Usually exemplified in a diagonal manner, cross holes can consist shapes like rectangles or squares. Perforated metals bearing cross holes are useful where you need better surface grip such s in industrial flooring.
ii. Diamond Holes: These holes provide a distinctive and aesthetically pleasing pattern finding use in applications like ventilation and filtration.
iii. Hexagonal Holes: These six-sided holes in perforated metals are frequently employed aesthetically like making architectural facades and artistic representations.
iv. Oblong Holes: Perforated metals featuring oblong holes are frequently utilized in applications that need increased airflow, including engine compartments or HVAC systems.
v. Round Holes: A common shape for perforations, round holes can be applied in filtration, ventilation, and ornamentation applications.
vi. Slotted Holes: Are long, narrow holes frequently utilized for drainage or filtration purposes. They can configured in either a vertical or horizontal orientation.
vi. Square Holes: These patterns are easy to implement.
Other designs may include slotted holes perforations on metals, and capsule hole perforated sheet metal. Remember, there are custom designs and shares. They will depend on your unique application requirements.
Chapter 4: Making Perforated Metals
When you punch holes in a pattern on a metal sheet, you have a perforated metal. While you can do this manually using simple hand tools, such an approach is not feasible for large scale use.
Making perforations on thinner metals (ideally those with larger gauge numbers) is easier compared to thicker metal sheets. Perforations can be presented in different designs called patterns using specialized machines such a punch and dies systems.
Here is how to perforate metals:
Prepare Sheet Metal for Perforation
The decision what metal material you need for your perforated metal project is dependent on use and availability. You also need to determine what material thickness is sufficient. These features determine the nature of the stamping process during perforation such as force required to achieve perforations.
Metal sheet thickness also determines the operation time when perforating and ultimately the quality. Furthermore, the choice of metal sheet determines the usage such as structural or decorative based on its material qualities.
Pattern Selection
While you have different patterning options for your perforated metal, the pattern choice can influence functionality. You can choose standard or intricate patterns.
Contrarily, robust functionalities such drainage and filtration will typically employ standard patterns such as square or rounded. You perforated patterns on metal can be:
- Staggered with finished
- Unfished ends where the latter allow continuity during installation.
Perforation
You can use many techniques including:
Rotary Perforation
A rotating drum featuring blades cuts holes into the metal sheet as it is conveyed through a cutting station. Rotary perforation can be easily implemented where the volumes are high due to the quick execution of the perforation process.
Laser Cutting
A laser stream is utilized as the cutting tool in laser cutting making it the only non-contact process. A computer program guides the laser to execute the cut pattern as fed by the computer aided design software.
Laser cutting is primarily useful in cutting perforated metals featuring complex shapes and patterns. A major advantage of laser cutting in perforating metals is the high finish quality achieved.
Punch and Die Perforation
A common method, it involves utilizing a punch press to punch holes into the metal sheets. The punch press consists of a die system in the shape of the desired hole pattern.
In this process, the metal sheet is placed on a flat surface whereupon a hydraulic press forces the dies into the sheet. The result is a clean-cut hole with minimal surface and edge distortion and burring.
Lubrication
The perforation process exerts immense frictional stress on the metal sheets given the applied forces and tool and workpiece interaction. In order to avoid surface damage and distortion, lubrication is necessary to cool the metal and prevent negative thermal effects.
Chapter 5: Critical Factors when Making Perforated Metals
Certain critical factors are essential when making perforated metals to ensure the resulting product conforms to industry standards. Some of these factors are discussed below.
Minimum Size of Hole Pattern
To estimate perforated hole size, you should consider material type and depth. For instance, when perforating aluminum and steel, it is common to ensure the metal thickness doesn’t exceed the hole diameter.
Pattern Direction
When making squared and rounded staggered perforations, it is typical to stagger them in the direction of the metal sheets width. Alternatively, where you have a row of straight holes, they should align with the metal sheet’s length.
For slotted perforations, you can present the slots with their length running along the metal sheet’s length or width.
Margins and Side Margins
It is typical to find perforated metals featuring margins with both finished and unfinished ends with the latter more common. In determining side margins, it is important to consider the edge last perforation separation distance.
Having a side margin combats distortion by reducing stress application during perforation.
For side margin, the breadth must not be massive. Usually, this prevent possibility of distortion.
Tolerances
Tolerances of perforated metals are stipulated the respective industry standards body and generally address the following parameters:
- The length and width of a metal sheet
- Perforation size
- Standard gauges or thicknesses
- The margins and camber
- Non-perforated areas
- Surface distortion and burrs
Chapter 6: Machinery and Equipment Used for Perforated Metals
Production of perforated metals has been made possible by using different machines with varying capabilities. Different factors affect the decision to select a certain machine beginning with the budget needs, work volume and the expected quality.
Expect to find any of the following mentioned machines in a metal working hub for perforated metals:
Rotary Pinned Roller
It has a big drum featuring extension that resemble a needle. These needles helps in metal perforation.
The drum rotates axially over metal sheets fed through a conveyer system impressing the pin structure on the metal.

Using a rotary pin roller is fast and capable of perforating several metal sheets in a minute and thus support large production volumes.
Punch Press Machine
Employs unique tooling purposed to cut metal sheets by punching or stamping into the desired shape via a die system. Different types of the punch press machine are available as follows:
- Wide Punch Press: It is the preferred option between the two that executes perforations by ramming metal sheets in single strikes. Due to its single action and capability to work with a feeding system, it’s utilized in large productions of perforated metals.
- XY-Axis: These machines encompass a ram with singular or multiple dies to punch out perforations while moving over the metal sheet. While the process takes longer since the workpiece is stationary, the machine can accomplish different shapes or patterns on one sheet.

Laser Machine
A laser machine achieves metal perforation by non-contact means by employing high power laser beams to cut through the metal sheet. The beam is regulated by programmed information achieved via computer aided design allowing very intricate shapes to be accurately cut.

Chapter 7: Factors Affecting the Cost of Perforated Metals
Several factors influence the cost of perforated metals and are therefore important when making a budget for your project. Furthermore, understanding these factors can help you choose the right perforated metal for your application while ensuring you get the best value for your money.
These factors are highlighted below as follows:
i. Metal Thickness: Producing perforations on thicker metal sheets requires larger force productions to penetrate the metal sheet. As a result, working on thicker metal sheets significantly influences costs.
ii. Metal Type: Different metals come at different cost with some widely available and thus affordable and others comparatively costlier. For instance, while aluminium is affordable titanium costs a premium.
iii. Perforation Technique: You can employ various techniques to cut patterns from metal structure. The equipment employed in laser cutting while highly accurate, are costly than tradition stamping/punching methods.
iv. Perforation Design: Encompasses the shape and size of the perforations where smaller and more intricate hole patterns are costlier and difficult to produce.
v. Perforations Distribution: Producing higher hole densities can be difficult requiring more complex machinery, and thus considerably increasing the cost.
vi. Surface Finish: Sometimes secondary processes such as surface finishing may be required after metal perforation. The finishing type you select will signify an additional cost to your project.
Chapter 8: Additional Processes When Making Perforated Metals
After extracting parts of your metal sheet to leave a desired pattern, you may refine the perforated metal further. As such, you can carry out secondary processes to further acclimatize tour product to the application.
Some of these processes are listed below:
Anodizing
When anodizing a perforated metal sheet, an oxide layer is formed over its surface to increase durability. The metal sheet is immersed in an electrolytic solution before subjecting it to an electric current.
Chrome Plating
Here, the perforated metal is plated with a thin chromium layer to augment corrosion resistance, durability, and appearance. It is typically used for aesthetic purposes and involves subjecting the metal to an electrolyzed solution containing chromium ions.
Corrugating
When corrugating perforated metal sheets, you create a series of parallel grooves or waves on the surface. Corrugating perforated metal sheets improves strength and durability while also courting aesthetic appeal.
Precision Leveling
Precision leveling allows you to flatten the metal sheet by removing surface imperfections resulting from the perforation process. Specialized equipment like the precision leveler achieve this aby applying force to the metal surface a controlled manner.
Resquaring
Resquaring corrects any distortion or warping that could have occurred in a metal sheet during perforation. During this process hydraulic or mechanical force is applied on the metal sheet to make it straight and flat.
Slitting
Slitting allows you to cut perforated metal sheets into narrower strips. A slitter utilizes blades to cut the perforated metal sheet along its length at an angle or in a straight line.
Shearing
With shearing, you cut or trim the perforated metal sheets by utilizing a sharp cutting edge to the metal. In shearing, you apply a downward force to the secured perforated metal sheet resulting in straight and clean cut.
Welding
You can join several perforated metal sheets by welding where you melt their contact points to permanently fuse the pieces together. There are different methods of welding, including: arc welding, gas welding, resistance welding and laser welding.
Top of Form
Top of Form
Chapter 9: Applications of Perforated Metals
The outstanding features of perforated metals ranging from strength, durability and aesthetic quality allow for its varied use. Some common applications of perforated metal parts are:
Architectural Applications
Architecture seeks to enthuse by visual stimulation objects or structures such as buildings, monuments and other man made features.
Food Processing
Food processing plants us perforated metal parts in grain screening. Additionally, they form part of food processing before packaging. Additionally, perforated metals can be used in making food production equipment such as baking trays and oven grills.
Construction
High strength metals such as steel are integral in construction projects given their highly enviable properties.
Its uses as such spans the following:
- Making warehouse and retail shelves for airflow and aesthetic reasons.
- Constructing temporary runways for airplanes.
- Making flooring and staircases in industries and plants.
- Used as ventilation grilles for air ducts in buildings.
- Roofing and ceiling applications for noise control.
Automotive Use
Use of perforated metal in automotive applications is not a novel concept but rather a standard over the years. Vehicle body modifications, radiator grilles, trade plates, and muffler guards are but a few examples.
Guarding Machinery
Using perforated metal is used to make guards for machinery which is useful in preventing injury to workers. Without these guards, injuries could arise from hot machine surfaces, moving parts such as conveyers and even flying objects.
Additionally, the perforation allows personnel to monitor the machines closely without putting themselves in danger.
Light and Heat Regulation
You can alter flow or transmission of solar light and heat. Through these perforated metals, you can achieve different effects.
For instance, when used in open air stadia, perforated grills minimize glare on both fans and players in the pitch.
Other systems such as HVAC use perforated sheet metals. This allows you to achieve thermal regulation at lower cost implication.
Industrial Flooring
Many industries employ perforated metal in constructing their flooring thanks to the durability of the metal and grip. Such unique flooring is essential in ensuring work place safety by minimizing slippage due to the oily and wet industrial environment.
Acoustic Control
The perforated metals play an integral role in soundproofing. With these accessories, you can manipulate the sound waves for unique application requirements. You can find these metal with perforations on speakers or sound boxes.
Electrical Shielding
Perforated metals are used to make Faraday cages to enclose electrical structures and/or systems sensitive to interference. Such constructions also allow for the flow of air to facilitate ventilation and prevent overheating of equipment.
Conclusion
Perforated metals are useful in diverse applications given their numerous outstanding features and qualities. You can convert any known metal type into perforated metal to suit your project needs and thus ensure success.
More Resources:
Perforated Metals – Source: IQS Directory
Perforated Sheet – Source: Wikipedia
Perforated Panel – Source: Science Direct
Perforated Sheet – Source: Metal Supermarket